APPLICATION OF THE TEST INKS/PENS
BLUE (17-07xx and 17-05xx) Pens and Inks
To make possible the printing and adherence of polymer plastics it is inherent that the surface be treated, so that the surface tension rises to a defined point.
Untreated PE and PP have a surface tension of about 30 dynes/cm. Well treated PE and PP should have a value of about 38-41 dynes/cm for printing.
Polymer plastics with a surface tension of less than 37 dynes/cm have binding difficulties. This is recognized in that the tape pull-off test has a negative result.
The value of treatment is tested by simply spreading the testing ink with the felt tip pen onto the surface. This testing method involves determining a dyne/cm level that does not change for a period of 2 seconds. Using Quicktest pen 38®S, spread the ink with the felt tip in a linear fashion onto the surface to be tested. If this dyne/cm level does not change for a period of 2seconds, then it has either the same or higher value.
This test pen is designed for personnel in routine testing purposes. It can give one a good insight of whether the material is being treated enough or not.
The testing inks evaporate quickly when the test pens are not kept closed. Therefore, immediate closure of the pens must take place after use. (The cap will “click” when properly closed.)
The surface tension is a definite criterion for the adhesion of printing ink onto PE and PP. Other factors exist such as exudation of lubricants that influence the adhesion of inks quite negatively, that in turn, do not necessarily register on surface tension testing. Consequently, even though good surface tension results were found, the printing ink adhesion can result negatively.
It is also possible, that polymer plastics with the same surface tension can give completely different printing ink adhesion results. In most cases, however, one can disregard these exceptions and get best possible results of printing ink adhesion with surface tensions of 38-41 dynes/cm. A surface tension value that is too low, approximately 34 dynes/cm, results nearly always in bad adhesion.
PINK (17-08xx and 18-08xx) pens and inks
- The pens/inks from 30 to 44 dyne/cm are brighter (the observation time here is 4 seconds)
- The pens/inks of 28, 29, and 45 to 60 dyne/cm are darker in color (the observation time here is 2 seconds)
This testing method involves determining a dyne/cm level that does not change for a period of 2 seconds. Using a middle value of 38 dynes/cm the testing ink is spread with the test pen felt tip in a linear fashion onto the surface to be tested. If this dyne/cm level does not change for a period of 2 seconds, then it has either the same or higher value.
The next higher value of 40 or 41 dynes/cm is then selected ad spread onto the surface. This method of testing is set forth until a testing ink breaks on the surface within a period of 2 seconds.
Should the testing ink break within 2 seconds with the 38 dynes/cm value, then lower values of the pens should be taken for testing the surface.
In this fashion, one is able to pinpoint the surface tension much easier and faster. Should the surface tension fall between 2 values, for example 36 and 38 dynes/cm, then with some practice it is possible to set the value closer to 36 or 38 dynes/cm.
These test inks are designed for personnel in routine testing purposes. It can give one a good insight of whether the material is being treated enough or not.
The testing inks evaporate quickly when the test pens are not kept closed. Therefore, immediate closure of the pens must take place after use. The surface tension is a definite criterion for the adhesion of printing ink onto PE and PP.
Other factors exist such as exudation of lubricants that influence the adhesion of inks quite negatively, that in turn, do not necessarily register on surface tension testing. Consequently, even though good surface tension results were found, the printing ink adhesion can result negatively.
It is also possible, that polymer plastics with the same surface tension can give completely different printing ink adhesion results. In most cases, however, one can disregard these exceptions and get best possible results of printing ink adhesion with surface tensions of 38-42 dynes/cm. A too low surface tension value, approximately, 34 dynes/cm, results nearly always in bad adhesion.
TESTING SURFACE ENERGY BY MEANS OF TEST INKS/PENS
General information
Each solid has a specific surface energy (SE) in its pure state, which declines due to impurities during the production and storage process. In many technical processes, such as gluing, painting and printing, surface energy plays an important role and determines the adhesive bond and wettability.
The SE is measured in mN/m (dynes/cm). This is displayed with test inks according to DIN 53364 and/or ISO 8296 or other compounds.
When compared to liquids or polymer melts, the SE of a solid can only be determined indirectly from the contact angle. In this case, a test liquid with a particular SE is applied on the solid.
Application of the test inks/pens
Metals: Assessing the cleanliness of the surfaces. Assessing the suitability of cleaning fluids.
Plastics: Determining the activation energy for further processing (e.g. when printing, gluing, painting, wetting).
Material | Metal, plastics, ceramics, etc. |
Impurities on the surface |
Oils, dust, antistatic agents, lubricants, release agents, fingerprints |
Surface cleaning/ treatment |
Plastics: with water, solvents, pre-treatments |
SE (untreated surface) |
Metals: 25-35 mN/m |
SE (treated surface) |
From 38 dyne/cm (minimum cleanliness value) |
Correct method of measuring surface energy of solids with test inks and pens
Measuring means | Inks and pens (available in Blue and Pink) Blue: harmful to health (18-70 mN/m) not harmful to health (72-105 mN/m) Pink: not harmful to health (28-60 mN/m) |
Carry out measurement with one type (color) of ink only! The inks are composed differently and can thus give different values; difference of up to 2 mN/m. |
Measuring temperature of environment and solid |
20°C | The SE decreases by approx. 0.1 N/m, when the temperature increases by 1°C and vice versa. |
Condition of the solid to be tested |
Cleaned; should not be touched with bare hands |
Even the tiniest layers of grease can change the SE. |
Application | Ink: Apply with a cotton-tipped applicator made of pure cotton. (in heavily soiled/oiled surfaces ) Use a new cotton-tipped applicator after each application Pens: Apply with little pressure. |
It is recommended to use this cotton- Commercially available cotton-tipped applicators (cotton buds) contain oils. Contamination particles can come off if excessive pressure is used during application of the ink, thus giving the wrong SE value. |
Applicable stroke length |
20-40 mm (as one uniform continuous stroke) |
|
Observation time | Blue: 2 sec (after application) Pink: 4 sec (after application; 30-44 dyne/cm); 28, 45-6- dyne/cm 2 sec |
|
Result | The following reactions are to be expected: 1. uniform continuous stroke 2. drop formation, (poor/no wetting) 3. Spreading of the ink |
The SE has reached the set value on the bottle or is higher. Not clean, repeat cleaning. SE is lower than the value of the ink SE is much higher than the value of the ink |
Shelf life | Blue: 28 – 72 mN/m -- 6 months Pink: 28-60 mN/m -- 6 months Blue: 18.4 – 26 mN/m, as well as 76 - 105 mN/m -- 3 months |
Individual components of the test ink evaporate at different rates. Close bottles and pens tightly after use. |
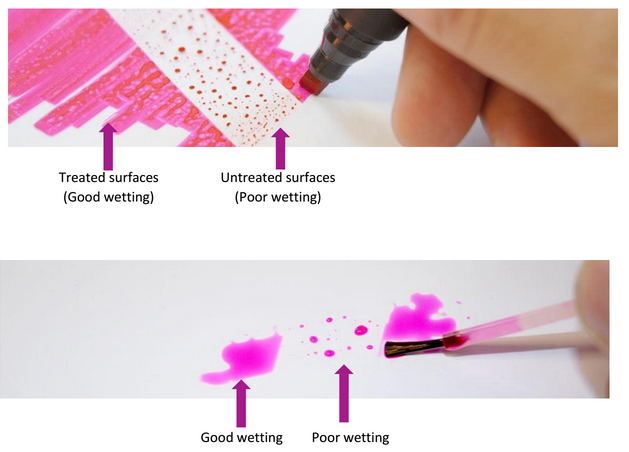
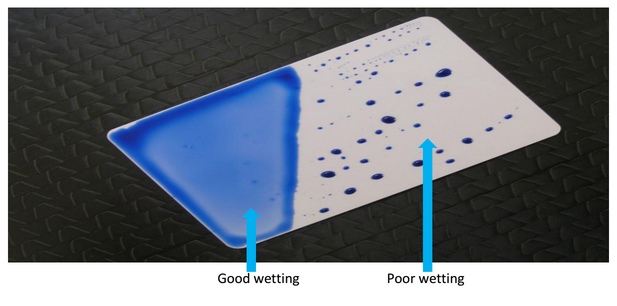
Call 920.465.6678
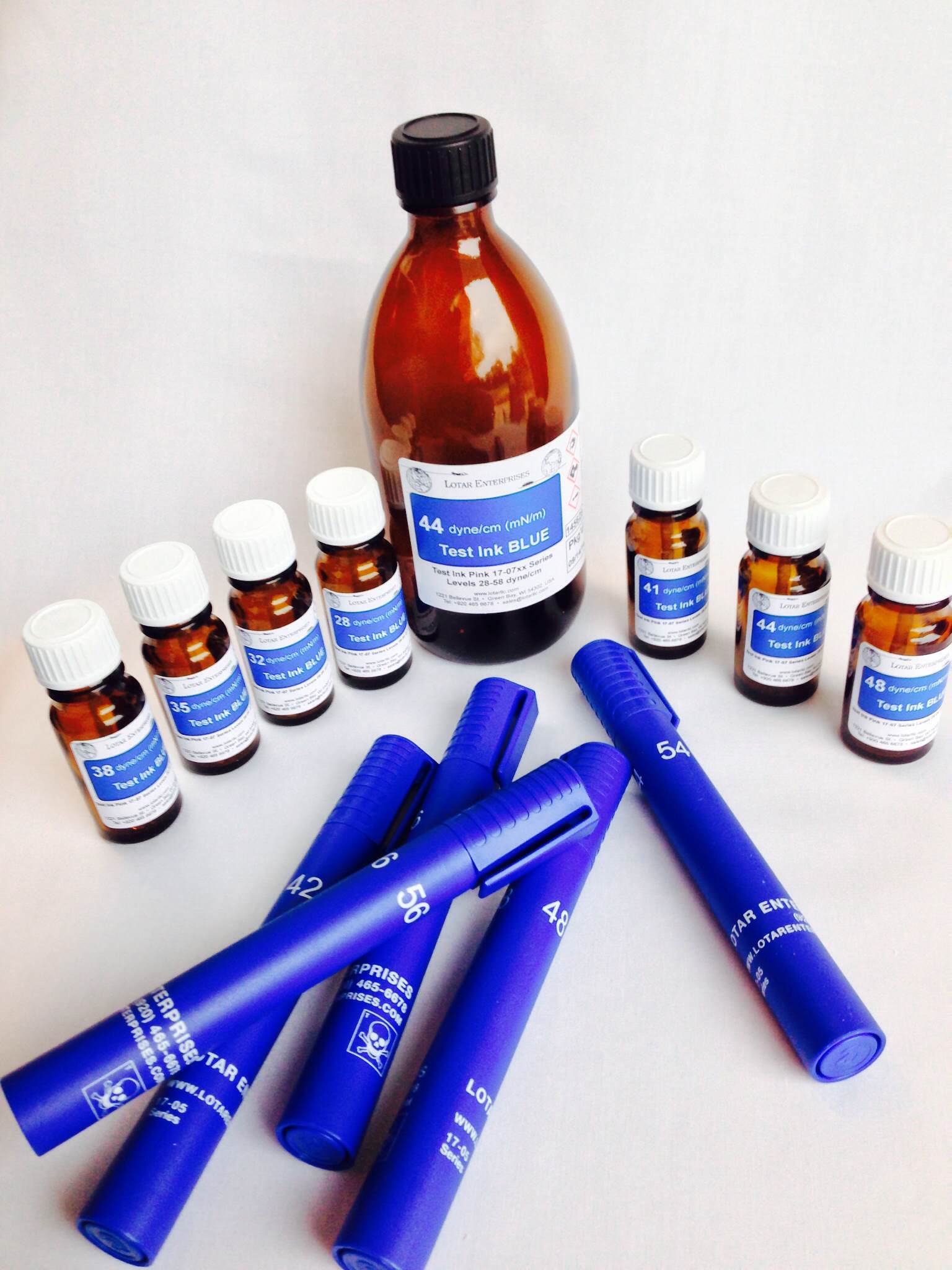
Questions?
Do you have a question, comment, or suggestion?
We want YOUR input!
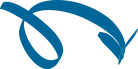
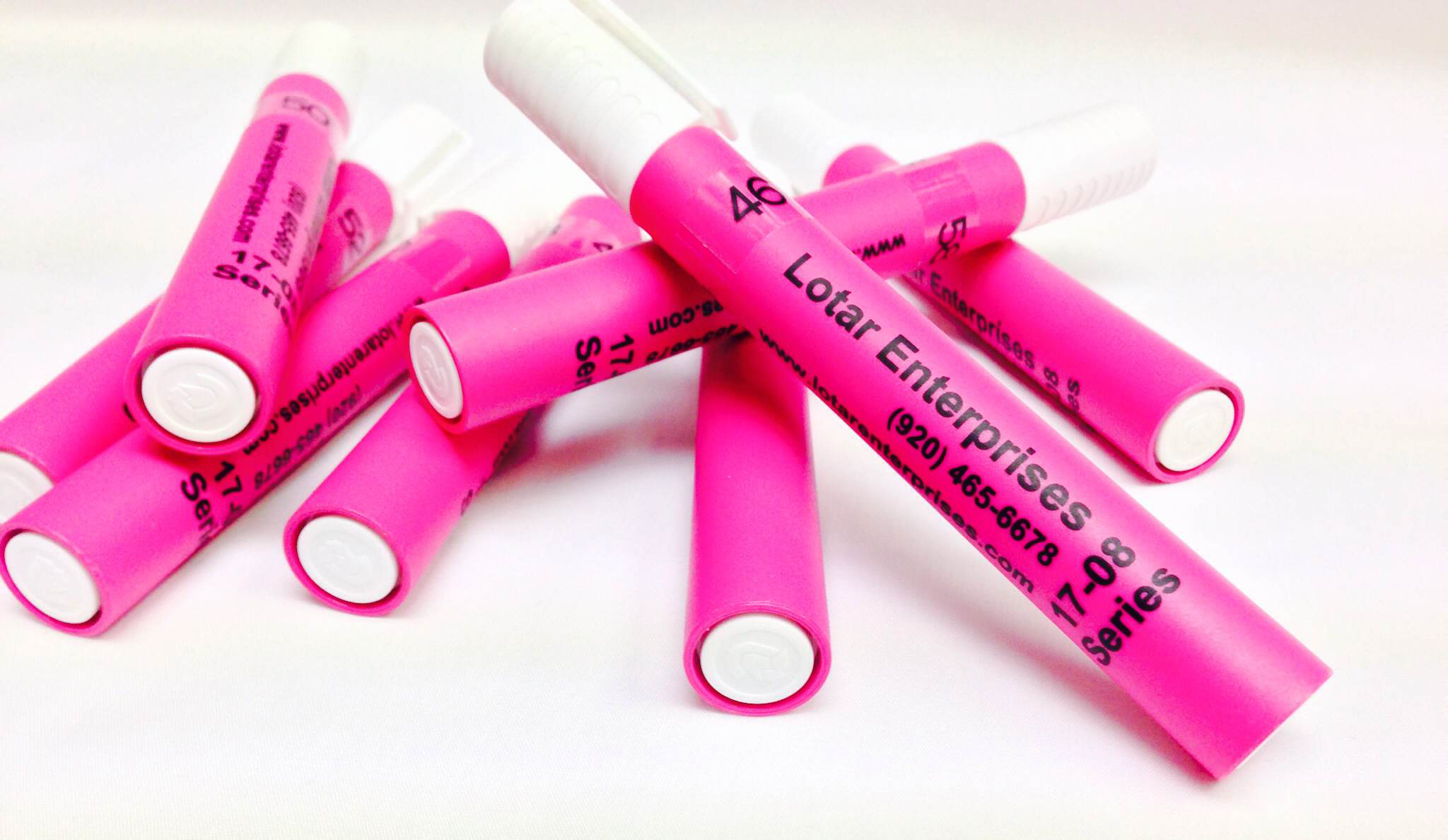